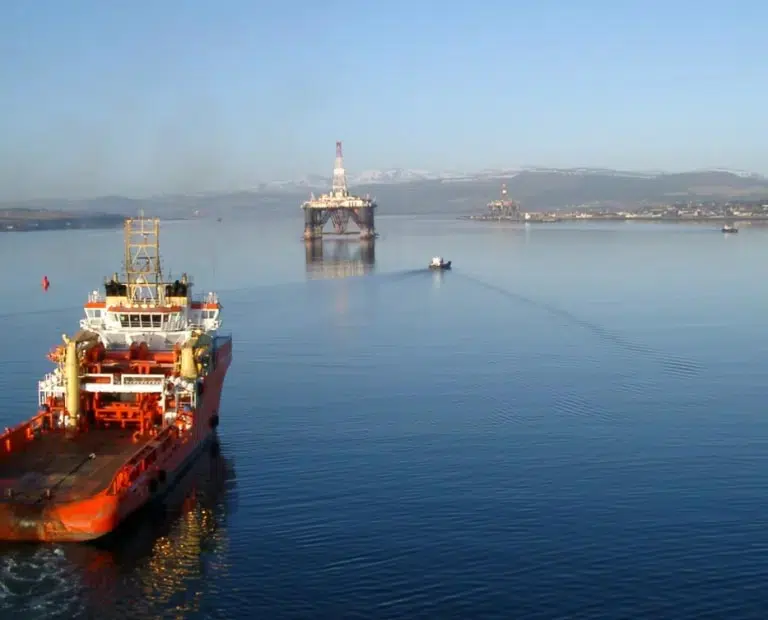
Access exclusive content
MOORINGS AND ANCHORS SOLUTIONS - REQUEST MORE INFORMATION
Complete mooring solutions.
Acteon’s solid domain knowledge in mooring design and offshore mooring operations spans the globe. We have installed some of the largest offshore assets in all water depths. We provide an integrated service covering the entire project lifecycle, from engineering, mooring design, procurement, and installation, through to maintenance and decommissioning.
Related Information
-
BlogWire rope is a versatile piece of equipment. In moorings, it can be used for motion...
-
BlogWhatever the energy requirement, MENCK, a marine foundations brand in Acteon’s...
-
BlogIn this blog, we review the use of Gravity Based Foundations (GBF) in offshore wind farms...
-
BlogWhen installing a suction pile, underpressure must be applied by an ROV’s pump to...